我国烧结矿中 MgO 含量变化现状及发展趋势
摘要: 在烧结工艺过程中,MgO 对烧结矿的冶金性能具有重要影响。随着烧结原料条件的变化及炼铁新技术的发展,烧结矿中适宜的 MgO 含量也随之改变。介绍了烧结矿的来源及作用机理,系统地分析了原料条件和炼铁新工艺对我国烧结矿中 MgO 含量的影响。相较传统的高碱度烧结矿 + 酸性球团矿的炉料结构,低 MgO 烧结矿 + 镁质球团矿结构下的高炉焦比、燃料比及渣比都有所降低,是未来炼铁的发展方向。
关键词: 烧结矿; MgO; 高炉炉料结构; 冶金性能; 镁质球团矿
近年来,随着钢铁企业的发展,烧结工艺水平有了很大地提高,主要体现在烧结矿质量、产量以及烧结过程和设备等几个方面。同时,烧结矿中 MgO 的适宜含量也发生了变化。MgO 含量变化对烧结矿的冶金性能影响显著,导致其在高温冶炼过程中的行为和作用也明显不同。由于钢铁企业之间的烧结原料存在巨大差异,因此在烧结矿适宜的 MgO 含量方面存在很大分歧[1 - 3],也使得改善烧结矿冶金性能的难度加大[4,5]。随着炼铁新工艺发展和设备条件的变化,低 MgO 烧结矿配加镁质球团矿已成为未来炼铁发展的新趋势。这种低 MgO 烧结矿配加镁质球团矿的炉料结构不仅可以满足高炉的冶炼要求,而且可以提高烧结矿和球团矿的冶金性能。简而言之,必须要不断优化烧结矿中的 MgO 含量,使其能最大程度地提高烧结矿的质量。
国内外高炉炉料结构如图 1 所示。由于技术水平和矿石来源的不同,世界各地钢铁企业的高炉炉料结构也有较大差异。在欧美,因其矿源多为细精矿,更适合球团矿的生产,因此高炉炉料主要以球团矿为主。例如,美国的 AKSteel 公司采用的就是球团矿比例在 90% 以上的炉料结构,因此美国高炉炉料中的 MgO 主要来自球团矿。中国高炉使用的绝大多数矿石为进口粉矿,而粉矿适宜烧结,这就决定了烧结矿是我国高炉炉料结构的主体。
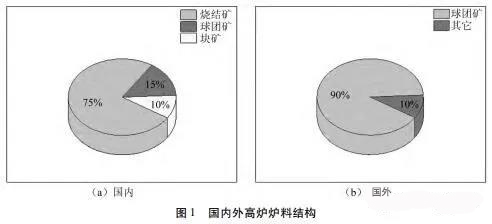
我国用于烧结生产的原料主要为铁矿粉、熔剂和燃料,某沿海地区炼铁厂烧结原料中 MgO 来源及含量百分比如表 1 所示。可知,烧结原料中的 MgO 大部分来自于白云石,其 MgO 含量为 20. 68% 。加入白云石的主要目的是: 得到一定碱度的烧结矿,使高炉冶炼可以不加或少加熔剂,以利于提高高炉冶炼强度、降低焦比。
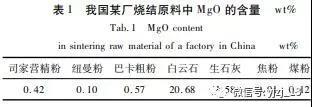
高炉冶炼过程受炉渣中 MgO 含量的影响较为显著,主要表现在: 可提高炉渣的脱硫能力和流动性,抑制炉内碱金属的循环积累,有利于改善炉渣排碱率等[6]。由于烧结矿中的 MgO 含量过高会影响其冶金性能,进而影响高炉生产,因此,当原料条件一定时,如何优化烧结矿中的 MgO 含量就显得至关重要。长久以来,MgO 作为高炉炼铁工艺的重要组成部分受到了广泛关注。烧结矿作为高炉冶炼的主要原料,其低温还原粉化指数( RDI) 是影响烧结矿品质的重要因素,不仅会影响高炉上部的透气性、高炉顺行,同时对能耗的影响也十分显著[7]。有研究表明[8],烧结原料中加入适宜的 MgO 在一定程度上具有抑制烧结矿低温还原粉化的作用。通常,MgO 对烧结矿有积极地作用,其可固溶于 2CaO ·SiO2 以稳定相变,提高烧结矿强度。当 MgO 适量时,液相流动性增强,玻璃相减少,可增加液相界面张力。但含量高于 4% ~ 5% 时烧结矿则不易熔化且伴有生料,强度降低[9,10]。熔滴性是烧结矿在高炉内的重要指标,适宜的 MgO 含量可改善烧结矿的软熔性能,提高高炉透气性,保证高炉顺行,提高高炉生产率。而还原性对熔滴性也有一定影响,一般来说,原料的熔滴性好,还原性也会好。因此,加入 MgO 可以达到降低焦比和节约原料的目的,获得更好的经济效益。
2 原料条件及工艺技术变化对烧结矿中 MgO 含量的影响烧结矿的化学成分对其质量的影响显著,当烧结工艺参数一定时,适宜的化学成分在提高烧结矿冶金性能的同时还能保证高炉的顺行,提高企业经济效益[11]。2. 1 原料条件变化对烧结矿中 MgO 含量的影响2. 1. 1 Al2O3 对烧结矿中 MgO 含量的影响2009 ~ 2017 年我国进口铁矿石的数量如图 2 所示。可知,近年来我国进口铁矿石数量显著提升,由 2009 年的 6. 3 亿 t 增加至 2017 年的 10. 75 亿 t,涨幅 70. 63% ,这都源于我国钢铁企业的快速发展。
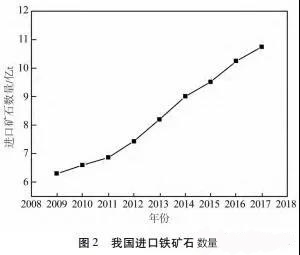
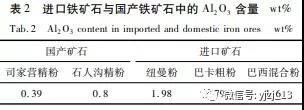
表 2 所示为部分进口铁矿石与国产铁矿石中的 Al2O3 含量。可知,进口铁矿石的 Al2O3 含量比国产铁矿石高,这会造成炉渣中的 Al2O3 含量相应增加,从而使得炉渣粘度增加、流动性变差,不利于高炉冶炼[12 - 14]。另外,Al2O3 含量的增加会提高烧结矿的低温还原粉化率。此时,在原料中加入适量 MgO 以形成镁橄榄石等多种高熔点物质,不但有利于提高烧结矿的低温还原粉化性能和软化熔融特性,而且因 MgO 具有一定降低高炉渣粘度的作用,可缓解因炉料中 Al2O3 含量增加、高炉渣粘度增大所带来的不利影响[15 - 18]。由此可知,随着入炉原料中 Al2O3 含量的增加,须相应提高并优化 MgO 含量,以最大限度地提高烧结矿的冶金性能,改善高炉冶炼条件。2. 1. 2 SiO2 对烧结矿中 MgO 含量的影响表 3 所示为 2015 ~ 2018 年沿海地区某炼铁厂烧结矿中 SiO2 含量变化。
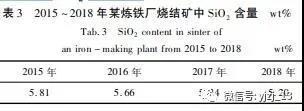
由表 3 可知,2015 年至 2018 年期间烧结矿中 SiO2 含量呈逐年降低的趋势,这源于低硅烧结技术的发展。迄今为止,我国大部分烧结矿都是高铁低硅烧结矿,一般品质较高的烧结矿中 SiO2 含量范围为 4. 8% ~ 5. 1%[19,20],其优势是: 有利于烧结过程中液相量的增加以及烧结矿的固结成型,改善烧结矿的还原性和高温冶金性能[21,22]。闫志武等[23]就 SiO2 对烧结矿影响的方面进行了研究,得出: 当 SiO2 含量在 4. 6% ~ 5. 9% 范围时,对烧结矿的低温还原粉化有抑制作用,其还原粉化指数随着 SiO2 含量的增加逐渐增大。张金柱等[24]的研究表明: 当 SiO2 含量为 4. 84% ~ 5. 0% 时,烧结矿中的铁酸钙及硅酸二钙减少,烧结矿强度降低。在烧结工艺参数及碱度一定时,适当降低烧结原料的 MgO 含量可促进铁酸钙生成,提高烧结矿强度,同时降低固体燃耗和返矿率,从而获得更好的经济效益。因此,当烧结矿中 SiO2 含量较低时,铁酸钙和液相量也相应较少,此时需适当降低 MgO 含量来缓解这一现象。目前,我国高炉炉料结构主要由高碱度烧结矿配加酸性球团矿以及部分天然块矿组成,其中烧结矿的 MgO 含量约控制在 1. 3% ~ 2. 3% [25 - 27]。高 MgO 烧结矿对高炉冶炼不利,而镁质球团矿则对其有改善作用[28]。低 MgO 烧结矿配加镁质球团矿是未来炼铁的新发展方向,此炉料结构不仅能满足高炉的冶炼要求,同时也可改善烧结矿和球团矿的性能。2015 年,某沿海地区钢铁企业采用了低 MgO 烧结矿配加镁质球团矿的炉料结构进行高炉冶炼,与常规炉料结构相比,烧结矿冶金性能如表 4 所示,高炉冶炼指标如图 3 所示。
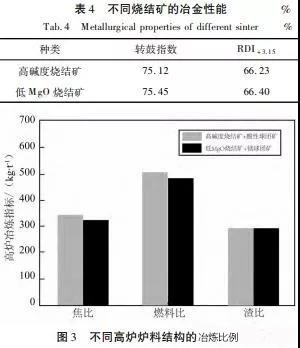